Our Story
Discover the journey of Rland, from our humble beginnings to becoming a leading cosmetic packaging solutions provider.
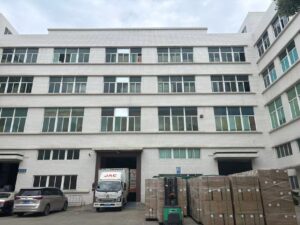
Company Foundation
Founded in 2008 in Shantou, China, Rland started with a vision to revolutionize cosmetic packaging. We established our first 4,000+㎡ modern production base, setting the foundation for what would become a comprehensive packaging solutions provider.
Development Timeline
- 2008 Established a 4,000+㎡ modern production base.
- 2010 Expanded international operations with a new export department.
- 2020 Reached a monthly production capacity of 5 million units.
- 2024 Embraced 3D printing and UV automation for enhanced surface finishing.
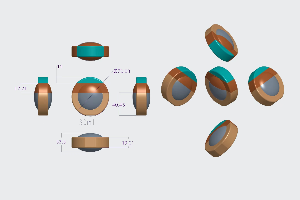
Mission & Vision
Our Mission
To provide innovative, high-quality cosmetic packaging solutions that enhance brand value while maintaining environmental responsibility.
Our Vision
To become the global leader in cosmetic packaging innovation, setting industry standards for quality, design, and sustainability.
Recent Developments
Production Capabilities
We've expanded our facilities with 10 additional injection machines and incorporated 10 industrial-grade 3D printers for rapid prototyping, allowing us to meet growing demand while maintaining our commitment to quality and innovation.
Surface Treatment Innovations
Our recent adoption of advanced techniques like hot stamping, silk printing, vacuum plating, UV spray, and gradient color effects has revolutionized our finishing capabilities, offering clients unprecedented aesthetic options.
Ready to Transform Your Packaging?
With our comprehensive solutions including design, mold development, mass production, and post-processing, we're ready to bring your vision to life.
Manufacturing Capabilities
Our state-of-the-art facilities and advanced equipment enable us to deliver premium cosmetic packaging solutions with precision and efficiency.
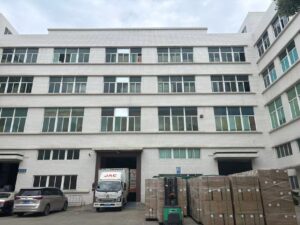
Facility Overview
Established in 2008, our modern production base spans over 4,000 square meters, equipped with cutting-edge technology and optimized workflow systems.
Equipment Showcase
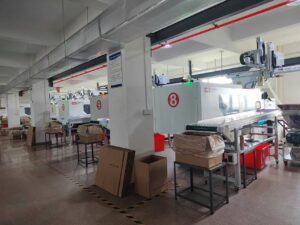
Injection Molding Machines
20 high-precision machines capable of producing complex designs with tight tolerances.
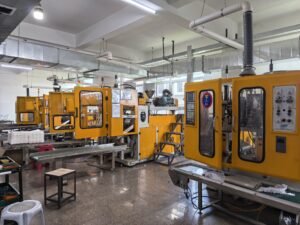
Blow Molding Machines
10 advanced blow molding machines for creating hollow containers with consistent wall thickness.
Silk Printing Machines
15 automated silk printing machines for high-definition, multi-color decoration on various surfaces.
3D Printers
10 industrial-grade 3D printers for rapid prototyping and small-batch production.
Certifications
Our commitment to quality is validated through rigorous international certifications that ensure our processes and products meet the highest standards.
Innovation & Technology
Pushing the boundaries of cosmetic packaging through cutting-edge technologies and innovative approaches.
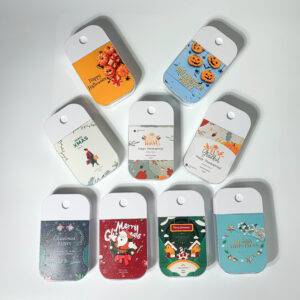
Surface Treatment Technologies
Our advanced surface treatment capabilities elevate the aesthetic appeal and functionality of cosmetic packaging:
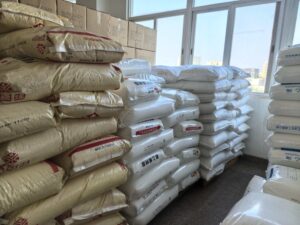
Material Applications
We specialize in a diverse range of materials to meet specific product requirements:
PE (Polyethylene)
Flexible, chemical-resistant, ideal for squeeze bottles and tubes
PET (Polyethylene Terephthalate)
Crystal clear, lightweight, perfect for transparent containers
PP (Polypropylene)
Heat-resistant, chemical-stable, suitable for hot-fill applications
PETG (Glycol-Modified PET)
Enhanced clarity and impact resistance for premium packaging
Design Innovation
Our design process combines creativity with technical expertise to deliver packaging solutions that stand out in the market.
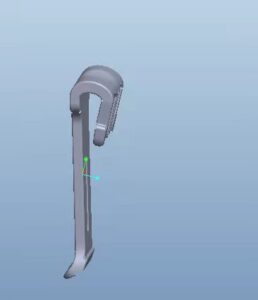
Rapid Prototyping
Our industrial-grade 3D printers enable 72-hour sample turnaround, allowing clients to visualize and refine designs quickly before committing to production.
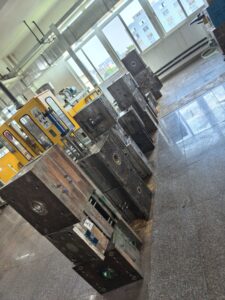
Custom Mold Development
Our engineering team specializes in creating precision molds that optimize material usage, reduce cycle times, and ensure consistent quality across production runs.
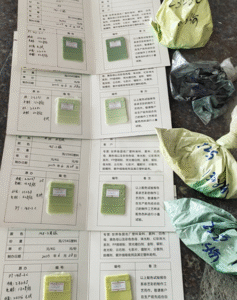
Color Matching System
Our proprietary color matching system ensures perfect consistency between design specifications and final products, maintaining brand integrity across packaging lines.
Ready to Innovate Your Packaging?
Let's collaborate to create packaging solutions that elevate your brand and delight your customers.